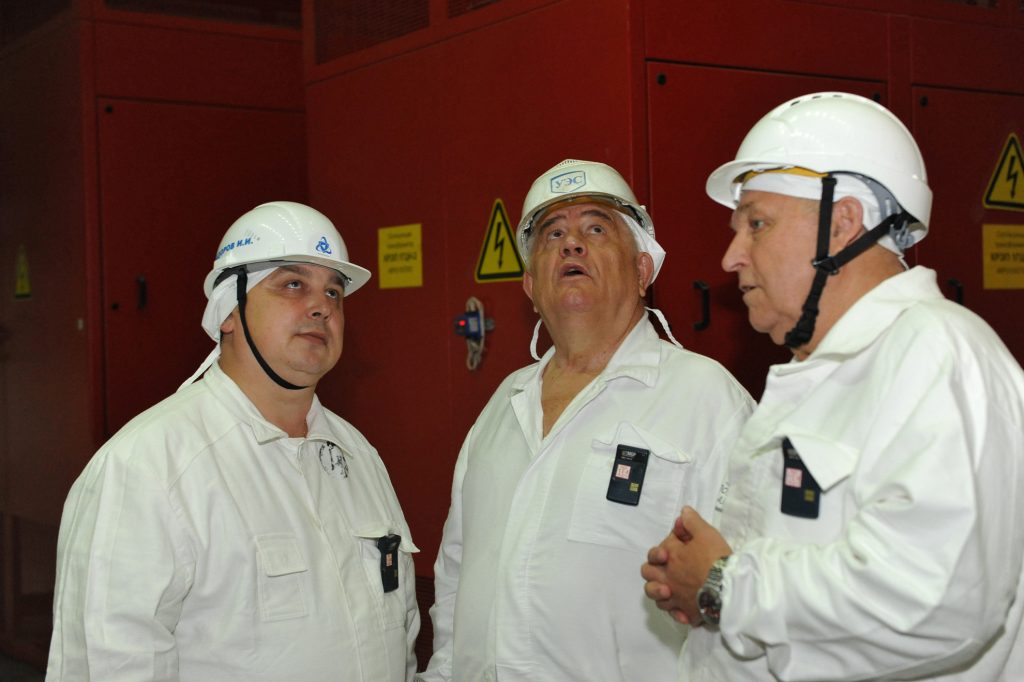
Фото: "Уралэнергострой"
О проблемах повышения качества управления при строительстве объектов использования атомной энергии, возможностях повышения эффективности работы мы беседуем с Виктором Сурудой, руководителем управляющей компании «Уралэнергострой»
– Виктор Борисович, почему строительство в атомной энергетике идет не так эффективно, как это задумывалось?
– Проводя анализ строительства различных объектов, следовало бы опираться на цифры – но к сожалению единой статистики нет. По крайней мере опираясь на некоторые данные из докладов руководителей строительного блока Концерна, сравнение недавних сложных строек Нововоронежской, Ленинградской АЭС и нашего энергоблока № 4 Белоярской АЭС показывает, что производительность труда у нас была значительно выше: численность коллектива не превысила 5 тыс. человек. В советское время для такой стройки потребовалось бы примерно вдвое больше. Я помню строительство БН-600; сегодня на Белоярской АЭС совсем другая стройка по культуре производства, по качеству, по технологиям. Мне жаль, что высокая оценка труда нашего коллектива за БН-800 хоть и высказывалась в частном порядке, не была озвучена на официальном высоком уровне.
Что касается последних энергоблоков Ростовской и Калининской АЭС, которые признаются удачными, их в общем ряду сравнивать не совсем корректно: опыт реализации проекта В-320 огромный, и опытные коллективы способны выполнить такую работу почти без вмешательства начальства; руководитель треста-генподрядчика может появляться на стройке раз в полгода, навестить коллектив в честь праздника. Но и ссылаться на преимущества серийного строительства, оправдывать этим проблемы головных блоков АЭС-2006 не приходится – наш объект на Белоярской АЭС тоже уникальный, в намного большей степени, чем те же новые энергоблоки ЛАЭС и НВАЭС.
Отличие нашей работы на Белоярской АЭС в том, что мы изначально организовали процесс управления строительством через полноценный генеральный подряд, и работали в тесном взаимодействии с заказчиком. Мы принципиально придерживаемся советского генподряда, но модернизировали его под рыночную экономику. Инженерную подготовку для субподрядчиков полностью взяли на себя: даже при сравнительно сильных производственных возможностях у субподрядчиков сегодня нет ни ПТО, ни Технического отдела. Нами было создано генподрядное предприятие и его дочерние структуры – которые раньше были отделами главного энергетика, главного механика, малой механизации и так далее. Было организовано предприятие «Атомстройтехника», задачей которого было всю технику сдавать по машиночасам субподрядчикам. Мы взяли на себя механизацию строительства, в том числе поставили на стройку все основные краны. Такой централизованный подход тоже эффективней по цене и производительности, чем мы наблюдали на других строящихся АЭС, – где набиралось огромное количество избыточной техники.
Около сотни электриков создали и поддерживали энергообеспечение строительства. Проект энергообеспечения был разработан и реализован настолько грамотно, что заказчик сохранил эту систему до сих пор и использует для собственных нужд; на ней же осуществлялся и пуск.
Наконец, для всех субподрядных организаций мы организовали новую систему контроля качества, и создали подразделение «Центр качества». Считается, что за качество должен отвечать заказчик, однако его роль возникает уже на этапе подписания объемов, а на всем протяжении строительства от разработки проектной документации и до реализации, контроль должен вести генподрядчик. Мы благодаря этому не получали больших претензий, не имели значительных переделок и убытков.
– В какой степени помогли современные строительные технологии?
– Действительно, успех работы на строительстве энергоблока с БН-800 во многом связан с возможностями современных технологий строительства, изучению которых мы посвятили время. Строительные конструкции энергоблока выполнены в монолитной технологии; объем составил до 500 тыс. куб.м. На Нововоронежской АЭС наши коллеги предпочли использование несъемной железобетонной опалубки: метод хорошо известный, но он сегодня и дороже, и менее производительный. Для изготовления несъемной железобетонной опалубки фактически необходимо создать отдельное производство, а качество конструкций проверить сложней.
На ЛАЭС-2 была выбрана монолитная технология, но работы проходили со значительными сложностями. Причин видится много – и проектные ошибки, и недостаточный контроль качества у некоторых подрядчиков, и невнимание к технологическим решениям. Почему наш опыт удачнее? Располагая (как и многие другие подрядчики) собственными бетонными заводами, мы вложили усилия в подбор подходящих рецептур бетона. Насыщение конструкций арматурой настолько плотное, что обычный бетон не проникнет на всю глубину, и потребовалось разработать свою рецептуру литого бетона (раствор отличается лучшей текучестью, а прочность затем не хуже обычного бетона). В добавках к бетону одним из основных компонентов стала зола Рефтинской ГРЭС, расположенной в нашем регионе; этот опыт еще советских времён позволил сократить расходы на импортные добавки. Впрочем, и зарубежных добавок мы тоже использовали немало.
Одно из важнейших решений – внедрение новой технологии стыкования арматуры, муфтовое соединение с обжимом. Мы понимали, что традиционная сварка ваннами крайне непроизводительна: один сварщик делает за смену лишь 5-6 таких соединений, да и сварщиков такой квалификации уже почти не найти; процент брака составит до 30 % – мы бы весьма отстали в сроках. Изучив в Англии технологию соединения резьбовыми муфтами, мы также её забраковали: были вопросы и к стоимости оборудования, и к качеству муфт. Да и результат не устроил: при испытании на разрыв не выдерживали именно соединения. Но оценив технологию обжима арматурных стыков, мы увидели, что производительность в десятки раз выше чем при сварке ванной; а случаи брака были лишь единичные, причем при испытании раньше разрывается арматурный стержень, а соединение выдерживает. Нет больших требований к квалификации при проведении таких работ: приспособление для обжима осваивается без труда, соответственно нет кадрового дефицита. Сегодня эта технология активно внедряется в России, и нашим коллегам по строительству атомных объектов следовало бы обратить внимание именно на неё.
Было выполнено много уникальных работ. Мы впервые организовали монтаж реактора и генератора параллельно со строительством: реактор был собран непосредственно на строительной площадке. Для этого мы смонтировали небольшой временный цех, обеспечили необходимые чистые условия и выполнили сборку реактора параллельно со строительством. Это позволило сэкономить время – как только была готова необходимая отметка 15 м, реактор можно было монтировать, параллельно со строительством здания. Впрочем, особенность других строек – в том, что реактор типа ВВЭР полностью собирается в заводских условиях и доставляется на площадку целиком, где уже монтируется.
Рекордом нашей стройки стали почти 12 тыс. км кабеля – пришлось укладывать в месяц по 600 км; следует заметить, что на стадии «П» предполагалось примерно вдвое меньше, но увеличение произошло из-за насыщения проекта автоматикой. Многое было бы можно сделать ещё быстрее и эффективней, если бы проектировщик внимательнее прислушивался к нам. В основе проекта разработка 1980-х годов, и менять её проектировщикам не хотелось; были и неточности, изменения проектных решений. Из-за этого нам пришлось просверлить порядка 30 тыс. отверстий для кабеля, а лишние затем заделывать вручную. Впрочем, наше решение именно сверлить отверстия современным инструментом помогло не потерять значительно времени – поскольку проектной организацией предполагалось выполнять отверстия с помощью закладных элементов, что менее производительно. Когда реактор был смонтирован и строительство стен завершено, здание мы накрыли бетонным куполом – площадью примерно с футбольное поле, это тоже уникальная работа.
– О проблемах РД и проектного комплекса в целом говорится на многих стройках. Каким образом помочь проектным институтам вернуться в тонус?
– Нужно изменить систему организации их работы; монстры – это главный тормоз строительства у атомщиков. Я однажды услышал, какой объем (на бумаге) делает не самый огромный проектный институт; в кубах бетона это было бы что-то запредельно огромное. Очень раздуты аппараты управления, а эффективность труда низкая. Поскольку оплата идет за лист – растет объем бумаги; а мы находим почти пустые листы. Эффективная численность организации – сто человек, один начальник; и проектировщики за рубежом уже разделились на малые организации, выбирают специализацию и эффективно конкурируют. Это уже произошло в строительном комплексе; в своё время именно через предоставление самостоятельности я спас «Уралэнергострой»: лучшие выжили, не лучшие прогорели, вместо них пришли опять же лучшие. Сегодня даже в пределах управляющей компании я дроблю структуру, чтобы центры ответственности сосредоточить в небольших коллективах, управляя ими на финансовой основе. Попытка руководить «монстрами» – это сразу потеря эффективности. Отсюда и реформирование проектной отрасли, как это происходит сегодня, у меня не вызывает оптимизма. Впрочем, проблема роста и усложнения аппарата – общая, она свойственна всем российским компаниям, причём при всём развитии аппарата часто получается, что решение всё равно принимает кто-то один.
Вообще сегодняшняя идея внедрить инжиниринг в управление строительством возникла, на мой взгляд, лишь по причине дефицита качественных генеральных подрядчиков. Лишившись генподрядчиков, наняли на управление строительством проектировщиков – и, будем откровенны, загнали и институты, и весь наш стойкомплекс в кризис. Рабочую документацию для строительства всегда делали ленинградский и московский «Атомэнергопроекты»; нижегородский институт опыта этой работы в подобном объеме никогда не имел – и в лучшем случае сможет присутствовать в процессе как руководитель высокого полёта.
Я полагаю, что реформа проектного комплекса должна быть такова: остаются несколько крепких институтов – генеральных проектировщиков, но существенно оптимизируется численность; из монстров по несколько тысяч человек должны выделяются в самостоятельные предприятия бывшие специализированные отделы. Они нанимаются на выполнение своих разделов, но работают в едином информационном пространстве, что позволяют современные технологии. А институты по нескольку тысяч штата, равно как и огромные тресты, ушли в прошлое. Ещё когда мы, «красные директора», ездили обмениваться опытом в США, там мне сказали хорошую фразу – «сила генподрядчика – в субподрядчиках»; когда же я сказал, что у меня 15 тыс. человек в 50-ти предприятиях, поинтересовались, почему я не в сумасшедшем доме. Вообще же, хоть плохая традиция раздувать огромную численность стара, нас в Минэнерго учили держаться за субподрядчиков; электрики и монтажники всегда были в привелегированном положении, даже квартиры получали раньше других. Американцы, как выяснилось, точно так же следят за субподрядчиками, вкладывают деньги в их развитие, обучают людей. Выбор подрядчика через торги – это «метод тыка»; кроме того, вредна система платить по минимуму – чтобы только выполнили задание; гораздо важней обеспечить заработок, но мотивировать на вложение в производительность и развитие. У нас же до сих пор политика на выжимание субподрядчика, когда он может выйти со стройки банкротом. Мы у себя сразу устроили учебный комбинат, хотя своих рабочих у головной компании нет – учили персонал субподрядчиков, а они это оплачивали. Словом, должен быть круг постоянных субподрядчиков, с которыми можно работать; только так на наши стройки придёт успех.
– Насколько эффективно выстроилось взаимодействие с заказчиком?
– Мы внедрили Производственную систему Росатома, ПСР – понимая ее по-старинному как научную организацию труда. Было реализовано несколько ПСР-проектов на стройке. Под влиянием заказчика, существенно подняли уровень безопасности производства и охраны труда: после нескольких несчастных случаев отладили систему обучения, инструктажа, контроля. Вообще заказчик в атомной отрасли отличается консервативным подходом, а строители более свободны в принятии решений – но именно сочетание консервативной среды и нашей активности дает лучшие результаты.
Сегодня, поскольку станцию сложно строить под ключ силами единого генподрядчика, и пока проекты не стали серийными, нужно идти известным с советских времен путем – через совместную работа заказчика и генподрядчика как единого целого. Заказчик обеспечивает проект (стадию «П»), но работает не со случайным генподрядчиком – а с теми, кто завоевал доверие, потому что элемент непредсказуемости выбора тендера в нашей отрасли недопустим. Генподрядчик должен включаться в работу на стадии проектирования – обеспечивая разработку РД – оптимально, нанимая проектировщика, но такого, которому может доверять, а не случайно выбранного на тендере. Хуже ситуация, когда приходится создавать подконтрольное проектное подразделение – это делается, если хорошего проектировщика не найти. Но в любом случае это эффективней, чем когда за рабочую документацию отвечает заказчик; лишь если генподрядчик непосредственно участвует в стадии разработки РД, получается комплексный эффект – и в сроках, и в оптимизации процессов, и в стоимости. Тем более что опытный подрядчик в атомной отрасли обучен консервативному, осторожному подходу в рамках правилах и инструкций. Что касается иногда звучащих упрёков заказчику в консерватизме – считаю, что на свободу творчества в атомном строительстве ссылаться нельзя. Мы, строители, должны подтягивать себя под все регламенты эксплуатации. Лишь это путь качественного и безопасного строительства.
– Поможет ли эффективности строительства идея «объединенного графика» как единого информационного пространства, где на нерадивого подрядчика можно будет незамедлительно воздействовать… методом кнута?
– Объединенный график в его сегодняшнем понимании будет работать в том случае, если будет представлять собою живую модель, формат проекта, в который смогут включиться субпроектировщики, заказчики и подрядчики. Вообще идеальный и единый сетевой график, охватывающий всю совокупность проблем строительства энергоблока, создать по моему опыту невозможно; мы проходили это как зарубежную моду ещё в советское время. Но единый график может работать как ориентир, как инструмент разделения задач на составляющие; 3D-модель в его составе позволит оформить картину зрительно. Но сможет ли она повлиять на сроки стоительства, на организованность – не уверен. В проектировании 3D-модель позволяет избежать столпотворения, чтобы одни сети не набегали на другие. Эти противоречия должны снимать субпроектировщики, работая в едином формате. В идеале мы как генподрядчик должны нанять субпроектировщиков: одному бетон, другому КМ, третьему электрику – и может быть лишь иметь в штате главных инженеров проекта, ГИПов, которые скоординируют их работу, в том числе в 3D. Но таких субпроектировщиков пока почти нет, и предстоит долгий процесс воспитания.
Собственно, система взаимодействия генерального подрядчика и проектировщика в советское время работала хорошо лишь потому, что мы руководили ими; я как главный инженер разных подразделений половину рабочего времени проводил в проектном институте; проектировщики тоже иногда дневали и ночевали на стройке. Согласовывали решения, и всё получалось. Но когда после долгого перерыва мы вернулись к работе с крупным проектным институтом в Санкт-Петербурге – вначале нарвались на позицию, «мы умы, а вы увы»: и нам потребовалось несколько лет, чтобы они вновь стали слушать нас. А слушали бы изначально – было бы и меньше издержек, и работа прошла веселее.
– А что показывает опыт других строек, за пределами «Росэнергоатома»?
– К сожалению, стройка комплекса МБИР в Димитровграде (по заказу НИИАР) пока не радует: есть неясности даже с основными параметрами проекта; прорабатывается задание для проектировщиков. Мы предложили подготовить проект здания с такими проёмами, чтобы туда можно было затем смонтировать оборудование, вес и габариты которого мы знаем пока лишь приблизительно; предлагаем принять за аналогию БН-800. Опять же, убеждаем заказчика поручить нам проектирование – поскольку если документация не появится, мы начнём отставать по срокам. Как бы то ни было, в данный момент никто кроме нас эту работу не понимает – ни заказчик, ни проектировщики. Я уже был бы рад, если бы проект выполнил Санкт-Петербургский Атомэнергопроект, так как несмотря на притирку мы всё-таки сработались; но как раз в силу организационных преобразований он сейчас отходит в сторону, и никто не понимает, как будет организовано проектирование.
За пределами рынка «Росатома» мы в России за последние годы построили ряд объектов – в том числе шесть парогазовых энергоблоков «под ключ». Это безусловно объекты не такие сложные, как наши атомные стройки – но мы тоже нарабатываем организационный опыт. Сегодня заказчики в нефтегазовой сфере стремятся к работе «под ключ», и нам отдают даже функцию заказчика, вплоть до подготовки эксплуатирующего персонала. Но опять же не все стройки проходят одинаково гладко. Нам повезло найти хороших заказчиков; мы заслужили у них авторитет и планируем дальнейшую работу. Надо впрочем заметить, что мы на уровень выше по сравнению со многими подрядчиками в теплоэнергетике именно благодаря «атомному» опыту; стандарты «Росатома» помогают нам оказаться лучше других генпорядчиков на этих объектах.
Также на стройках за пределами «Росатома» нами без сложностей освоено ресурсное ценообразование – оно удобнее, чем до сих пор действующий в нашей отрасли базисно-индексный метод. К сожалению, насколько мне известно, сборника наших отраслевых расценок так и не сделано. Сегодня мы составляем сметы традиционным методом лишь для получения денег от заказчика, а со своими субподрядчиками давно ведем расчеты ресурсным методом. Это удобнее, быстрее, и давно должно быть реализовано в атомной отрасли в полном объеме.
– Есть ли нарекания к системе образования, подготовки кадров?
– По большому счету нет; молодежь сейчас лучше и активней, чем были мы сами, жизнь их заставляет учиться и работать. Мы обучили в Уральском Политехническом университете человек 60 для собственных нужд; вузы безусловно не в лучшем состоянии, но если их целенаправленно поддерживать и чётко ставить задачи, то они способны давать неплохой результат. Хорошая подготовка сохранилась в техникумах, но проблема в том, что хорошие выпускники школ предпочитают институт – и соответственно некоторые профессии, где важно именно специальное образование, испытывают дефицит качественных кадров – электрики, монтажники. Впрочем, что-то можно решить с помощью учебных комбинатов; да и технологии сегодня упростились, стали проще для освоения. Это раньше мастер прятал свой рецепт, секрет – а теперь все эти секреты приобретаются хотя бы под марками строительных смесей.
– Один из путей повышения эффективности взаимодействия заказчика (инвестора) и подрядчика – это введение позиции «инженера-консультанта», как фигуры, балансирующей интересы сторон. Приходилось ли сталкиваться с таким подходом?
– Такой подход действительно внедряется и в России; но это делают те заказчики, которые не имеют возможности нарабатывать собственные компетенции в строительстве, и уже в достаточной степени успели возненавидеть слово «генподрядчик». Не секрет, что ряд крупных структур, с громкими столичными именами, успел набрать неудачный опыт: стройки дробятся, затягиваются, делается много ненужного. Во многих случаях это по неумению, кроме того иногда затянуть стройку – это увеличить свою прибыль. Поэтому заказчик и нанимает консультанта, который проводит поиск (учитывая и цену, и качество, и опыт) и предлагает заказчику подрядчика по строительству (нередко именно наш «Уралэнергострой»!), а также отсекает ложные экономические интересы (они могут быть и у заказчика тоже). Я сталкиваюсь с инженерами-консультантами преимущественно как посредниками между иностранными и нашими компаниями, например когда используется зарубежное оборудование. Но всё-таки для заказчика такой подход – это отказ от самостоятельного знания рынка, и форма сложения с себя ответственности.
Алексей Комольцев для журнала «РЭА»